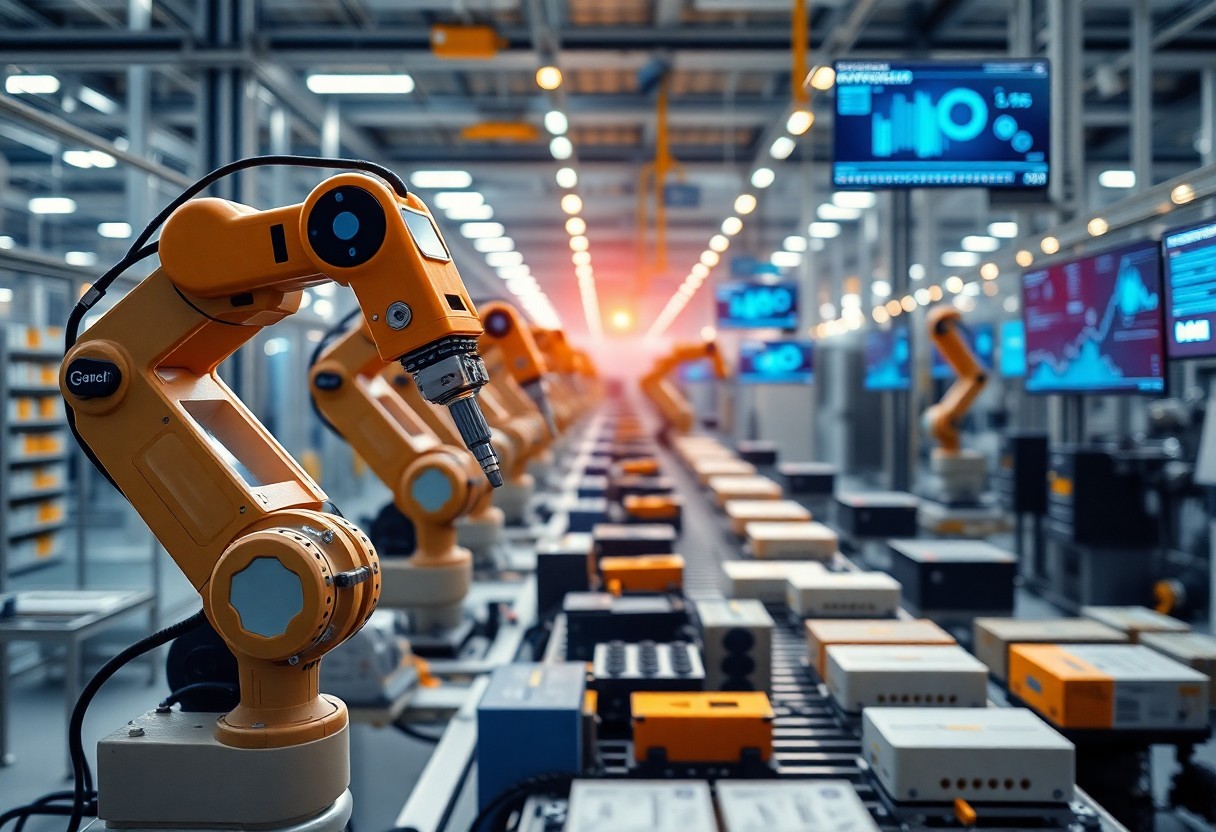
Manufacturing industries are rapidly evolving, as Smart Factory Intelligence integrates artificial intelligence (AI) into production processes. You now have the opportunity to enhance your operational efficiencies, reduce waste, and improve product quality through innovative AI applications. While embracing this transformation can provoke concerns over job displacement and cybersecurity threats, the positive impact AI can have on decision-making and predictive maintenance is undeniable. This blog will guide you through how AI revolutionizes your manufacturing landscape, enabling smarter operations and sustained growth.
Revolutionizing Production Lines through AI
AI’s infusion into manufacturing is redefining production lines by automating complex processes and enhancing precision. Machines equipped with advanced algorithms analyze historical data to optimize workflows, dramatically increasing output while reducing waste. Companies adopting these AI technologies experience not only significant cost savings but also improved product quality. For instance, manufacturers implementing AI-driven robotics have reported up to a 30% increase in production efficiency, showcasing the tangible benefits of integrating smart technologies into traditional manufacturing environments.
Enhancing Operational Efficiency with Predictive Analytics
Predictive analytics empowers manufacturers to anticipate equipment failures before they occur, leading to substantial reductions in downtime. By leveraging historical data and machine learning algorithms, you can identify patterns and anomalies that suggest when maintenance is required. This proactive approach not only keeps production running smoothly but also extends the lifespan of your machinery, further enhancing your operational efficiency.
Real-Time Monitoring: The Rise of Smart Sensors
Smart sensors are revolutionizing how you monitor production processes by providing real-time data on various parameters, from temperature to vibration levels. With their ability to track and report critical metrics instantaneously, these sensors help you identify potential issues before they escalate, allowing for timely interventions. As a result, production quality and efficiency see marked improvements.
The integration of smart sensors in production lines exemplifies AI’s transformative impact on manufacturing. These devices collect and transmit data continuously, enabling you to gain insights into machine performance and environmental conditions. For example, a leading automotive manufacturer reported a 25% reduction in defect rates after implementing smart sensors to monitor assembly processes. Additionally, real-time alerts prompt immediate action to prevent equipment malfunctions, ensuring that production schedules remain uninterrupted. This synergy between AI and smart sensors leads to a more agile manufacturing environment, where adapting to changes and maintaining high-quality standards become second nature.
Data-Driven Decision Making in Manufacturing
Leveraging data analytics is transforming how you make decisions in the manufacturing space. Data-driven decision making allows for real-time insights, enabling you to optimize processes, improve productivity, and significantly reduce operational costs. By harnessing vast amounts of data collected from machinery, sensors, and supply chains, you can identify trends, forecast demands, and enhance inventory management. In doing so, your organization becomes more agile and capable of responding to market fluctuations, ultimately driving profitability and growth.
The Role of Machine Learning in Quality Control
Machine learning is fundamentally reshaping quality control within manufacturing. By training algorithms on historical quality data, you can detect anomalies and predict potential defects before they impact production. This proactive approach not only enhances product quality but also minimizes waste and rework costs. For instance, manufacturers implementing machine learning techniques have reported defect reduction rates of up to 30%, allowing you to maintain a competitive edge in quality assurance.
Bridging Gaps: Integrating AI with Legacy Systems
Integrating AI with your existing legacy systems is necessary for maximizing efficiency without a complete overhaul. Many manufacturers often face challenges with outdated infrastructure that isn’t designed for seamless AI integration. Implementing AI-driven solutions can be done incrementally, allowing you to enhance systems gradually. For example, using an API to connect your legacy machinery to AI analytics can facilitate data sharing, improving operational insights while retaining your current system’s value.
As you explore the integration of AI with legacy systems, consider your automation and analytics avenues. Legacy systems often utilize proprietary formats, making it necessary to develop custom middleware that translates data into machine-readable formats. Depending on the complexity, this could involve detailed planning, investment in skilled IT resources, and testing. However, successful integration leads to real-time monitoring, predictive maintenance, and ultimately, smarter operations without abandoning the foundational systems you rely on.
Workforce Transformation: Human-AI Collaboration
Collaboration between humans and AI is reshaping the workforce landscape in manufacturing. As AI takes over repetitive tasks, employees can focus on higher-value activities, promoting innovation and efficiency. This transformation not only enhances productivity but also requires workers to embrace new technologies and skillsets, blending their expertise with AI capabilities.
Redefining Skills and Roles in Smart Factories
In smart factories, traditional roles are evolving as AI and automation play a pivotal part in daily operations. You will find that your job may shift from hands-on tasks to more analytical or creative responsibilities, requiring proficiency in data interpretation and AI interaction. Upskilling becomes important, empowering you to navigate the changing landscape confidently.
The Cultural Shift: Adapting to an AI-Enabled Environment
Adapting to AI integration calls for a significant cultural shift within organizations. Embracing a mindset of continuous learning encourages collaboration and innovation, allowing you to thrive in an ever-evolving ecosystem. It also fosters an atmosphere where human insights and AI solutions work in tandem to drive excellence.
The transition to an AI-enabled culture invites you to rethink how you approach your work environment. In this new paradigm, fostering open communication about AI’s role can mitigate resistance and empower you to be a part of the digital transformation journey. Emphasizing creativity alongside technology, companies can cultivate an agile workforce ready to tackle challenges and explore opportunities that AI presents. For example, organizations like Siemens and General Electric have effectively prioritized employee involvement in AI strategy, resulting in enhanced morale and productivity. By positioning yourself as a proactive participant in this transformation, you not only secure your place but also contribute to the organization’s competitive edge.
Ethical and Security Considerations in Smart Manufacturing
Incorporating AI into manufacturing introduces a myriad of ethical and security challenges that must be navigated carefully. Your approach not only impacts operational efficiencies but also raises questions around data privacy, job displacement, and the overall societal implications of autonomous systems. Establishing effective ethical frameworks and security protocols is crucial to ensure that advancements in technology contribute positively to your organization and community.
Navigating Data Privacy and Cybersecurity Challenges
Data privacy and cybersecurity are paramount in smart manufacturing. With the integration of IoT devices and AI systems generating immense amounts of data, vulnerabilities may emerge. Protecting sensitive information from breaches becomes a top priority, as reports indicate that 60% of small to medium-sized enterprises experience cyberattacks. Implementing robust security measures, including encryption and regular audits, helps you mitigate risks associated with data breaches while ensuring compliance with regulations like GDPR.
Addressing the Ethical Implications of AI Deployment
Deploying AI in manufacturing raises ethical considerations, particularly concerning job displacement and decision-making transparency. You face the challenge of finding a balance between optimizing productivity and maintaining a responsible workforce. Conducting regular assessments of AI impacts can help identify potential workforce shifts and create training programs for reskilling employees.
The ethical implications of AI deployment extend beyond job displacement; leveraging AI’s capabilities without transparency can lead to biased decision-making. The 2020 AI Now Institute Report highlighted that algorithms may inadvertently reinforce existing biases, resulting in unfair treatment of employees or customers. To address this, incorporate ethical guidelines and diverse stakeholder input in your AI design process, ensuring fair outcomes. Engaging regularly with your workforce to understand their perspectives enhances trust and fosters a collaborative environment, ultimately supporting responsible innovation. By proactively addressing these ethical dimensions, you position your organization not only as a leader in smart manufacturing but also as a responsible member of the global community.
The Future Horizon: Trends Shaping Smart Factories
The landscape of smart factories is rapidly evolving with numerous trends that will shape the future of manufacturing. From predictive maintenance to customizable production lines, converging technologies are paving the way for unprecedented operational efficiency. As you navigate these advancements, embracing adaptability will be key to harnessing the full potential of smart factories and maintaining your competitive edge.
Industry 4.0 and the Internet of Things Revolution
Industry 4.0, fueled by the Internet of Things (IoT), is revolutionizing how smart factories operate. By connecting machines, sensors, and systems, your factory can share real-time data, leading to enhanced visibility and control. This connectivity enables predictive analytics, facilitating proactive decision-making that minimizes downtime and boosts productivity.
Emerging Technologies: Beyond AI in Manufacturing
While AI plays a significant role, other emerging technologies are vital for the future of manufacturing. Advanced robotics, for instance, enable greater precision and efficiency in assembly lines, while blockchain enhances traceability and security in supply chains. Augmented reality (AR) and virtual reality (VR) provide immersive training experiences, improving workforce skills and engagement.
Exploring these technologies reveals their potential to transform your manufacturing processes. With advanced robotics, for example, repetitive tasks can be performed with unmatched speed and accuracy, resulting in increased output. Implementing blockchain technology offers a secure, transparent way of tracking materials and products, enhancing trust among partners. Moreover, AR and VR not only enable remote assistance for troubleshooting but also provide interactive training modules that can significantly reduce onboarding times and improve employee proficiency. As these technologies continue to evolve, they will complement AI solutions, driving further innovation in your smart factory journey.
Conclusion
From above, it is clear that Smart Factory Intelligence is transforming the landscape of manufacturing through the integration of AI technologies. You now have the opportunity to enhance your production processes, improve efficiency, and drive innovation by embracing these advanced solutions. By leveraging data-driven insights and automation, you can optimize your operations, reduce costs, and increase your competitive edge in the market. As you explore these advancements, your factory can evolve into a smart ecosystem, ready to meet the challenges of the future.